Multi-step Routing Checklist
Multi-step Routing Checklist
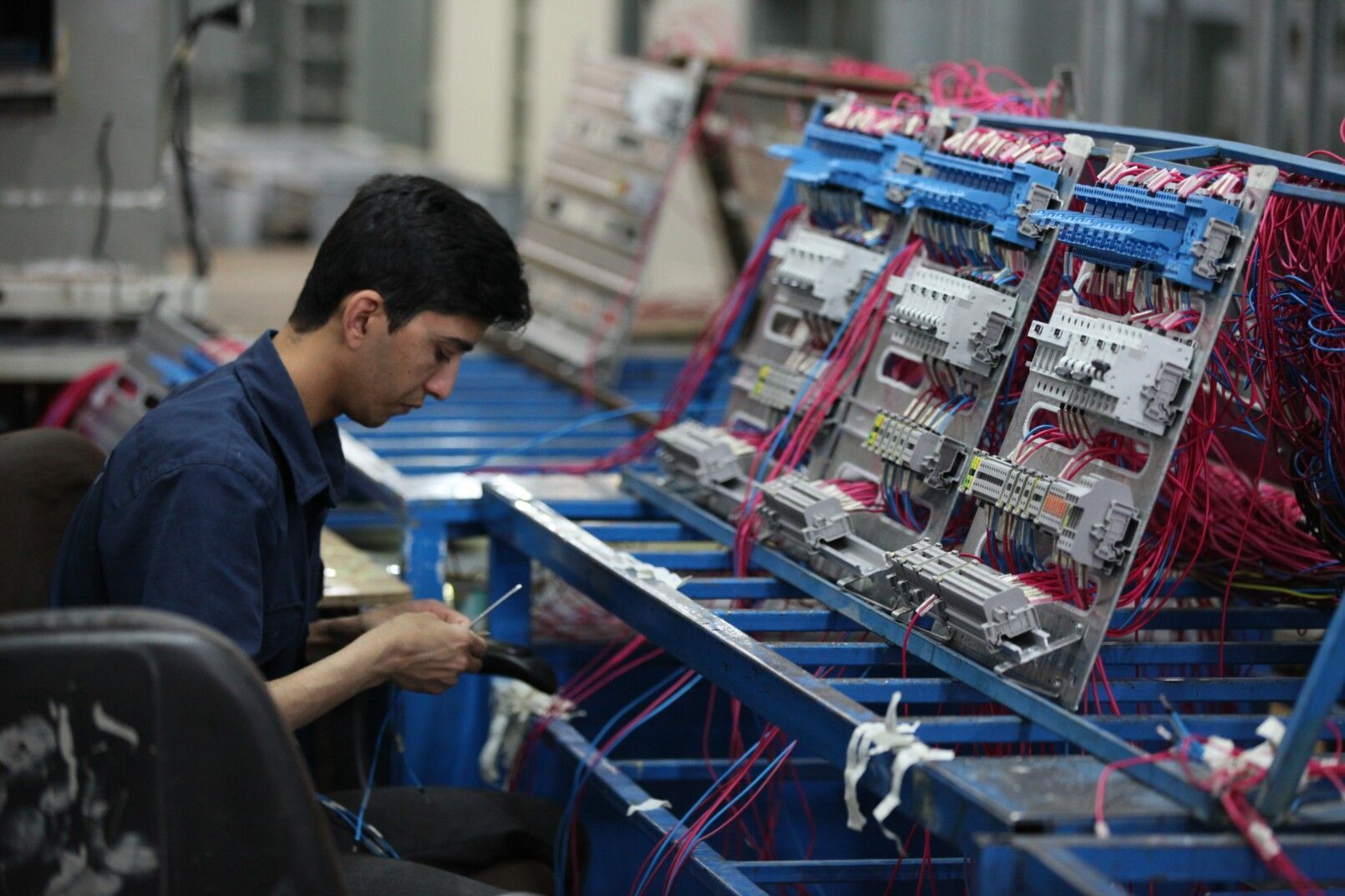
Initial setup if you are using multistep routing.
Multi step routing – If you use the optional multi step routing extension, then you should configure work cells and routes. If you are not using this feature, anyway your system will have one cell and a single step route for this cell.
All products will use this single step route.
By default both the cell and the route have the same name as your company identifier. Prior to adding data for manufacturing items, carry out these additional steps. For fuller details please consult the documentation for the Production section.
When setting up features for planning, note that loading can be measured on either “per work/machine item” basis or “per cell” basis. Cells should primarily be used for tracking work flow. Manufacturing cost codes can be used to measure what work has been done without the need to create work items or cells for particular simple operations. When in doubt keep it simple in the first implementation of multi step routing.
Step | Manu Online |
---|---|
1. Enter the time unit you wish to use, called the “period”, and the normal length of a working day. For instance if you wish to use “minutes” per item in your product structures, then specify number of minutes per period as 1 and number of periods in a day as 480 if work is done on an 8 hour day. (This is the default) | Admin -> System settings -> System settings tab |
2. Create manufacturing cost codes (if you plan to record work times) These codes are optional, but allow you to record “what” people have been doing inside a work order without the need to specify cells and steps for work flow. | Admin -> System settings -> System settings tab |
3. Specify your work cells The system is created with one work cell which is named with your company id. Create more work cells according to the design of your factory. Work cells are typically physical areas in your factory for which you wish to monitor the flow of work orders and view loading and perhaps capacity. At this stage, just create the work cell and description. Do not add capacity records. | Production -> Factory setup –> Work cells |
4. Create route templates The system is created with one route which is named after the company id. Create more routes according to the main process flows of your product families. (It is generally not a good idea to create a route for each product.) Each step of a route must be on a cell. As the steps are added, the screen may show a warning tha the route is not defined properly. To have a properly defined route ensure that each step is referred to by a previous step or is a start step. Specify the “Ready on day” number as the number of days of through put time typically used by products using this route. | Production -> Factory setup –> Routes |
5. Create items for work and machine timeDecide the different work and machine time items that will be needed and create them. On their properties tab specify the Standard cost per period. This will be used in work orders as part of the calculation of the manufacturing cost of a product. It is recommended to create as few work items as possible, perhaps only one. Create more than one if you have significantly different costs for different people or if you have people with certain skill sets for which you need to monitor capacity. Create separate work items with a higher cost if you wish to track overtime costs in manufacturing. | Sales – Items – New |
6. Update cells with work and machine time capacityCapacity is set by specifying the start date of the capacity, the number of periods per day (default is minutes), days per week and multiple. Multiple is the number of people or machines that are in the cell. So if there are two people fixed to one cell working an 8 hour day and period unit is 1 minute, the specify 480, 5, and 2 in the grid. This is optional. If you do not enter capacity figures, you can still see loading. Particularly for people, specifying capacity per cell is not relevant as people can move between cells as needed. In this case the production planner work be working with factory level loading. | Production -> Factory setup –> Work cells |
7. Update product structures with work and machine time items Include the work and machine time items in the manual creation or import. Remember to specify the correct step for each. The number of units per item is specified in point 1 of this list. Default is “Minutes”. | Sales – Items |
8. Create a list of Operators (aka employees, workers)Work time recording is done by “operator”. This is so that computers can be shared inside a work area and each operator does not need to have a separate login to the system. In many cases companies have one computer per work cell. Specify a work item for which the operator’s time will be recorded to a work order if using automatic work time collection. Work items are specified for normal time, overtime, Saturday time and Sunday time. Specify a unique ID for the operator. This will be used if barcoding of work time is in use. Optionally specify a PIN number for each person. This is used for entering work time or clocking in and out. | Admin -> System settings -> System settings tab -> Operators |
After completing this initial setup, you can start creating sales orders and using the system. Remember that while the system is in “demo mode” it is possible to empty it of all orders (from Admin-> Start-up wizard) so that it is possible to practice order entry.
Get in touch today about your manufacturing challenges.
We work with Xero.